0755-81710691
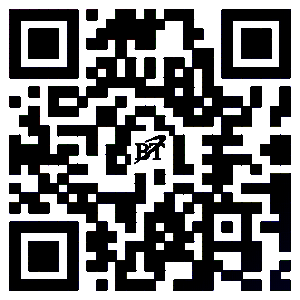
手机: 13925271184
邮箱:z609665418@163.com
官网:http://www.szbist.com/
地址:深圳市龙华区观澜街道大富社区平安路58号共联富基创新园5栋201
18650电池分选机为何能有效加速锂电行业升级?
发布时间:2024-12-17 17:35:52当我们谈及新能源与移动电子产品时,18650型锂电池一直是一种广为人知的存在。小到笔记本电脑、大到动力电池组的应用,都能看见它的身影。在庞大的生产与使用规模之下,电池一致性与质量稳定性尤显重要。此时,18650电池分选机扮演了关键角色。人们不禁好奇,这台装备究竟起到了怎样的作用?又是怎么在快速发展的锂电行业中扮演“精准把关者”的?以下从不同角度展开,逐层剖析其核心功能、运作原理以及未来发展的新思路。
一、18650电池分选机的重要背景
1. 行业需求的提升
随着汽车电动化和数码设备多元化的快速推进,18650型电池的生产规模持续扩张。对于动力电池厂商而言,不仅要提高产能,更要保证质量。电池的一致性、容量、内阻等性能参数直接决定了电池包的寿命与安全。假如缺乏高效准确的分选过程,就会让不良品流入下游环节,增加后期检测及返工成本。
2. 市场对品质的不断聚焦
移动设备、电动工具与储能系统的用户越来越注重电池续航时长与安全稳定性。若在出厂前就能将性能稳定的18650电池分门别类,加以筛选并统一分组,不仅能有效降低后续故障率,还能在用户端赢得更好的口碑。基于这个现实诉求,18650电池分选机在流水线上的地位已经从“可有可无”变为“必不可少”。
3. 自动化工厂的崛起
传统人工分拣模式下,不仅速度慢,而且准确度难以保障。人工操作时间一长,疲劳与疏漏在所难免。自动化工厂趋势日益明显,各种数控设备和机器人逐渐替代人力。18650电池分选机的应用恰恰呼应了这一趋势,带来更高效率和更少差错。
二、核心工作原理与技术亮点
为了理解18650电池分选机的实质价值,不妨先看它的运作逻辑。从上料到数据记录,各个环节都通过机械、电气与测试软件结合来实现自动分拣。
1. 机械与自动化结合
设备往往由上料系统、传送线、测试工位及分拣输出单元组成。电池在传送线上有序流动,到达测试工位后接受容量、内阻、电压或极性的检测。根据采集到的数据,由中控系统判断它应分配到哪个料道或分选盒子。机械手或拨动机构随后会自动把电池送往相应的分选区域,整个过程几乎不需要人工干预,做到了快速分拣和精准定位。
2. 电气测试精准化
18650电池的分类通常基于容量、电压与内阻等核心指标。一台可靠的分选机需要高精度、低误差的测试仪表,比如采用四线制内阻测量方法、程序控制检测时间与放电电流等。对不同厂商的电池或不同批次的产品,可以依照设定的分档规则完成筛选。测试过程严谨且重复性好,也意味着它在大规模流水线作业中能保持较高稳定性。
3. 数据采集与存储
设备自带的数据采集系统不仅能测得每颗电池的测试参数,还能自动保存各项信息,甚至生成统计报表,供质量与生产管理部门查看。借助工业以太网或无线通讯,分选机可接入上位机或MES系统,让企业在工厂层面实现数据互通,便于后续调度和品质追踪。
4. 安全保护与工控软件
电池测试过程中还要关注安全隐患。短路保护、过流保护,以及ESD(静电防护)等手段必不可少。工控软件通常具备自检与报警功能,如遇分选机构卡顿或者电气异常,系统会发出警报并自动停机,以防问题进一步扩大。
三、从多维度论证分选机的价值
分选机之所以能在18650电池生产流程中扮演越来越举足轻重的角色,正是因为在高效、质量控制与成本管控等多方面带来直接收益。
产能与效率的飞跃
依靠人工分选时,每分钟的分拣数量有限,而且人工持续高强度作业也并非长久之计。自动化的18650电池分选机每分钟可处理数十至上百颗电池,大幅提升车间效率。尤其在当前产能压力不断加大的背景下,更快的分拣速度显然成为一道“救命符”。
质量稳定性与一致性
电池分选机可将不同容量和内阻的电池精准分档,比如容量不达标、内阻过大的电池会被直接识别并剔除或进入相应的低档分类箱,从而保证最终封装的电池包内部性能基本保持一致,这对大规模应用场景至关重要。减少了组装环节因性能差异带来的不良率,也降低了后期售后服务或召回的风险。
人力成本与安全隐患降低
全自动分选系统能代替人工的繁重操作,工人数量相对减少。企业可将更多精力投向研发或市场开拓,而不是把人力集中在流水线上。随着操作风险降低,工厂安全事故的概率也会有所下降,进一步带来生产管理的良性循环。
信息可追溯性
自动采集的分选数据可以同工厂MES、ERP系统对接,形成数字化生产链。今后哪怕出了质量问题,也可通过数据库回查具体批次的测试结果,以及当时分拣工位的数据参数,大幅缩短故障溯源时间,并帮助企业在工艺层面持续优化。
四、设备选型与应用思路
要让分选机真正发挥作用,还得结合企业自身的情况来做合理的选型与布局。不同企业在产能、测试标准、预算和空间规划等方面都有差异,因此分选机选择更需要多重考虑。
测试精度和分选效率匹配
高精度意味着设备的内部测量仪器更先进,但成本也相对更高。如果企业主要生产普通消费级18650电池,可能无需用到最高精度的测试仪表。但若是为动力电池或高端储能市场服务,精度就显得格外重要。
设备兼容和自动化水平
通常希望设备能兼容不同厂商或不同批次的电池。针对一些方形或异形电池的后续扩展,可优先考虑具备可调工装夹具的机型。自动化水平越高,对产线整体的衔接越流畅,但也意味着对操作人员技能有一定要求,在设备调试和日常维护方面要做好充足培训和储备。
占地与人机交互
工厂空间有限时,应尽可能选用结构紧凑、布局合理的分选机。另外,机器界面通常配备触摸屏或上位机交互界面,能让操作员清晰地查看实时测试数据、料道状况和报警信息。易用性和安全性也同样不可忽视。
售后支持与硬件备件
一旦分选机出了故障,需要快速诊断并恢复生产。部分设备商提供远程协助功能,可以在线诊断软件与电路模块的问题。如果所在产线上对连续作业要求很高,还要确保备件供应及时,否则将会影响整体生产节奏。
五、延伸场景与系统化布局
18650电池分选机虽聚焦在电池检测与分类,但它在整条锂电池生产线中并非孤立存在。与之配合的前后工序,如容量测试、充放电老化以及PACK组装等,往往需要通用或专用设备协同。透过系统化思路来设计生产流水线,能最大化挖掘分选机的潜力。
前道与后道设备的协同
通常在分选机前会有充放电柜或老化测试设备对电芯进行初步筛查;而在分选机后,合格的电芯再进入PACK环节做进一步组装。如果能够将这几个步骤在物料流与信息流上打通,那么从上料到下线就可以形成无人化或少人化的连续作业,大幅降低中间等待时间。
自动物流与生产调度
若对接AGV或自动传送线,把电池从老化柜运送到分选机,再把分选后的电池运往其他工位,就能构建一条高效又紧凑的生产线。这种方式对于产能逐渐扩大的工厂非常友好,只要硬件接口和数据通信协议兼容,后续扩展或改造也十分顺畅。
数据管理与质量追溯
分选机输出的数据记录到工厂的数据库中,可以与制造执行系统(MES)或企业资源规划系统(ERP)进行对接。管理层或工程师可以通过后台快速获取生产实况,了解良率和班组效率等指标,并据此改进生产计划。万一有批次异常也能借助数据回溯找到根源。
六、未来发展趋势与新思考
更加灵活的参数化设置
随着不同厂家对18650电池的定制化需求增多,分选机需要更加灵活的编程与参数设定。如果可通过人机界面或远程软件,对分选规则(如容量分档和内阻分档)进行灵活修改,那么面对多批次、多规格电池也能轻松切换。
多样化兼容与高速分选
18650并不是锂电行业唯一规格,未来一些工厂可能转向21700或4680等更大尺寸电池。为了兼容更多型号,分选机设备或许会采用可换轨道、可调夹具等方案。针对产能大幅提升的趋势,也可能出现新一代高速分选机,每分钟处理电池数量达到更高水平。
智能化自诊断和运维
除了分拣电池的功能,行业也有望看到具备自我诊断能力的设备。一旦感应到机械部件松动或电气传感器异常,机台能在故障变严重前报警并建议保养计划。这种主动式维护,可以极大减少停机时间。
与AI检测相结合
人工智能在图像识别和数据分析上都有很强的优势。不少企业尝试在分选机中引入视觉检测功能,通过摄像头对电池外观进行识别,辅以算法检测表面缺陷或刻印信息。结合测试数据与图像特征,可以实现更全面的质量把关。
追随固态电池与新材料的脚步
市场对锂电池升级换代的呼声越来越大,固态电池或半固态技术正在酝酿中。虽然具体规格与工艺尚未定型,但分选机也需要跟进相关技术演化,储备适应新型电芯外观和测试方法的技术方案。此类前瞻布局有助于在下一轮行业变革中抢占先机。
七、全局性价值和总结
18650电池分选机不仅在日常生产中帮忙分拣良莠不齐的电芯,更承担了控制品质与保障安全的关键使命。从效率提升到资源节约,从系统集成到智能化管理,它与锂电工业自动化发展的潮流息息相关。多年前,许多企业还需要大量人工对电池做简单电压筛选;如今,一台高精度分选机便能取代繁琐人工作业,极大缩短生产周期并提升良品率。
当市场需求日益旺盛、产品规格和性能要求不断变化,分选机本身的不断升级演进就成了必然趋势。一方面,设备研发方在技术层面持续深耕,不断提高测试速度与精度;另一方面,工厂在引进设备的同时,也会着眼于自动化产线和数字化管理的整体布局。通过软硬件的有效结合,每一颗18650电池都能得到最适合的分选归类,最终产出更安全、更高性能的成品电池。
而展望未来,随着智能生产模式在更多领域普及,18650电池分选机或许只是整个锂电生态链自动化大军中的一员。新型电池规格的冲击、性能检测维度的丰富,都将倒逼设备迭代。在这个进程中,如何在确保生产效率和品质之余,最大限度地降低运维和人工参与,则是所有锂电企业要共同应对的课题。分选机的出现无疑给出了一个可行思路——借助自动化和数据化的力量,让产品质量管控与生产规模扩张实现“双赢”。未来,它有望与更多先进技术深度融合,将电池制造推向更高层次的工业革命之中。